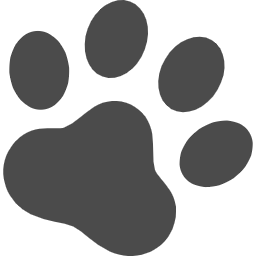
コンクリート工事の施工管理を徹底解説!公共工事で評価を得る方法まとめ
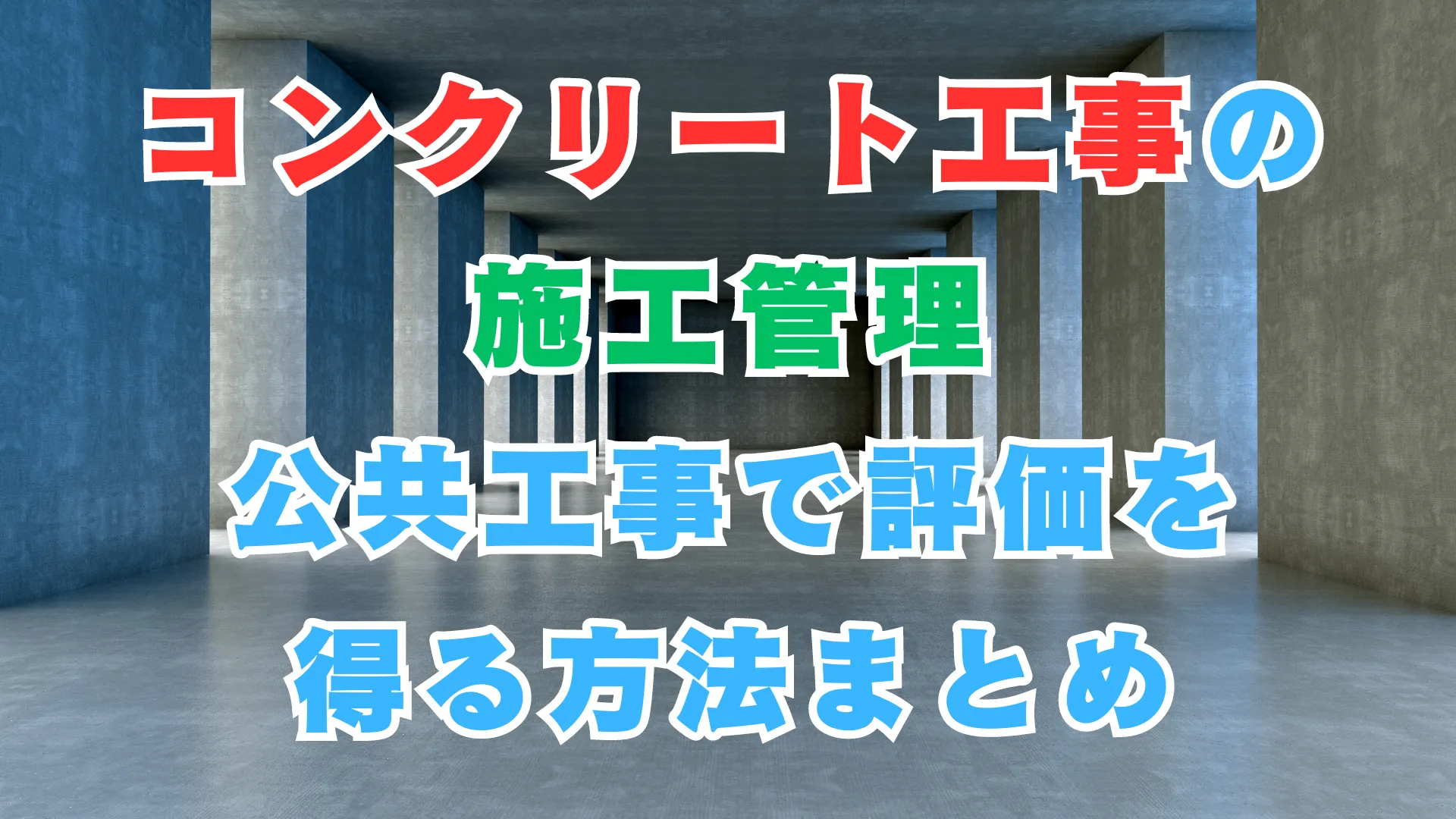
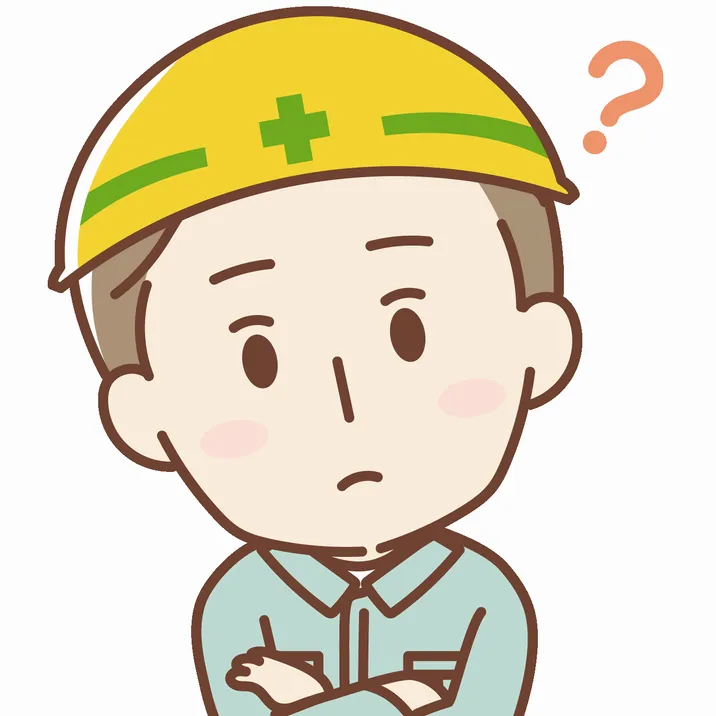
コンクリート工事の施工管理で大事なことは把握してるつもりだけど、検査の時に困らないように復習しておきたいな。
こんなお悩みに答えます。
コンクリート工事は施工計画をはじめ、事前の準備無しではトラブル連発もある工事。
本記事では、国交省や都道府県など公共工事でのコンクリート工事の施工管理について、土木学会コンクリート標準示方書の内容を基に、写真・図解・表・グラフを使ってわかりやすく解説します。
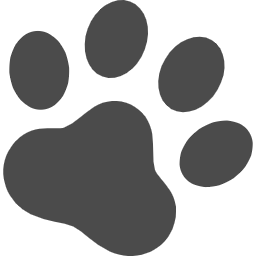
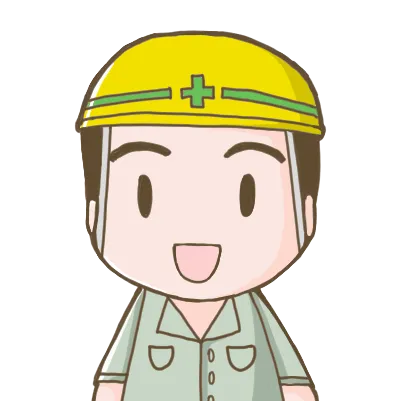
現場で後輩に「コンクリート工事の施工管理を詳しく教える時間が無い!」って時にも、本記事が使えますよ。
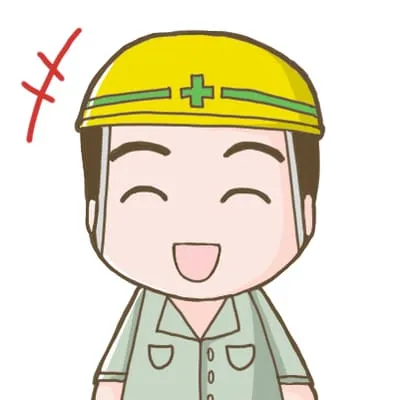
当サイト『ゲンプラ』の運営者:ランメイシ
現場監督と家庭(プライベート)の両立を応援するために、土木工事の施工管理をやっている現役の現場監督(歴16年)が当サイトを運営。施工管理業務の悩みに全力でサポートします!ご安全に!
保有資格:1級土木施工管理技士、河川点検士
主な工事経験:河川の築堤・護岸工事、道路工事、橋梁下部工事
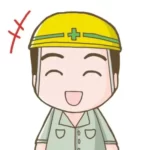
当サイト『ゲンプラ』の運営者:ランメイシ
現場監督と家庭(プライベート)の両立を応援するために、土木工事の施工管理をやっている現役の現場監督(歴16年)が当サイトを運営。施工管理業務の悩みに全力でサポートします!ご安全に!
保有資格:1級土木施工管理技士、河川点検士
主な工事経験:河川の築堤・護岸工事、道路工事、橋梁下部工事
施工計画:生コン打設で失敗しないための準備と管理方法
建設現場での仕事は、色んな予想外の出来事に対応する必要があります。
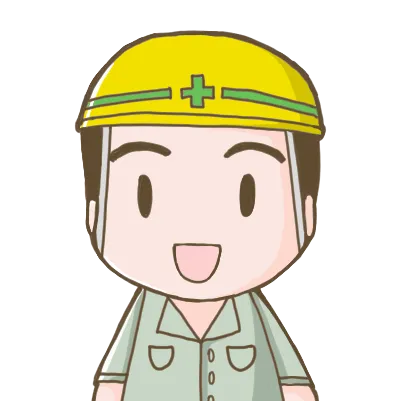
小さいことを含めれば、現場でいろんなトラブルを経験してますよね。
何が起ころうとも準備万端でいることが大切です。
それは何故かと言うと、建設現場では様々なトラブルが起こりうるからです。
- 突然の雨が降ってくる
- 修理したはずの機械が壊れる
- 交通が混雑する
- 図面に無かった地下埋設物が出てくる
これらの状況は、工事に影響を与える可能性がありますよね。
経験豊富なベテラン監督は、長年の経験から様々な状況を見極め、問題解決につながるアクションをとることができます。
コンクリート構造物に不具合が起きたら大変ですが、経験豊かな技術者ならこれを防ぐことができます。
そして、計画通りに進まないことを前提に、余裕をもった施工計画を立てることも大切です。
なぜなら、現場ではいつ何が起きるかわからないからです。
このように、建設現場では常に変化に対応できる準備と経験が求められます。
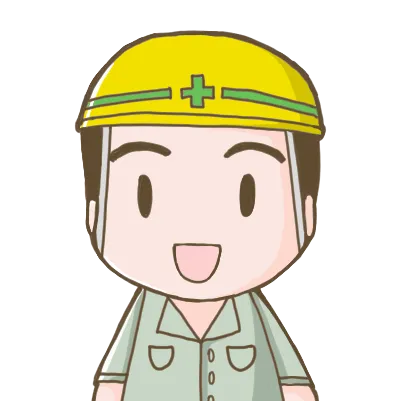
結論をおさらいしますね。
建設現場での仕事は予期せぬ問題に直面することもありますが、技術者の経験と余裕を持った計画があれば、それらの問題も乗り越えることができます。
何が起ころうとも準備万端でいること、それが建設現場での成功への鍵です。
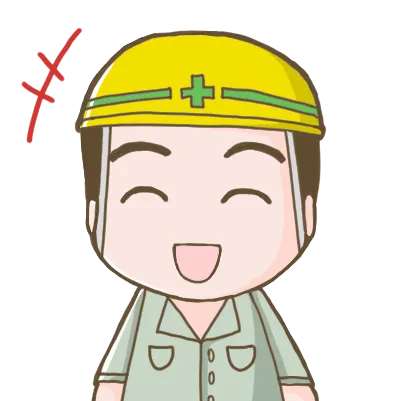
何も無い状態からコンクリートの準備を整えるのも大変だと思うので、チェックリストを作りました。ぜひ参考にしてくださいね。
関連記事 【チェックリスト配布中】生コン打設で失敗しないための準備と管理方法【施工計画編】
生コンの発注:上手な工場選びと契約のノウハウ
建設業界において、生コンの適切な使用は品質を左右する重要な要素です。
生コンを上手に使うためのポイントについて総括します。
- 品質管理
- 生コンの品質は工場での製造から現場での使用まで一貫して管理する必要がある
- 適切な品質管理は安全で耐久性のある建築物を作る上で不可欠です
- 原材料の品質確認
- セメントや骨材などの原材料の品質が、生コンの品質に直接影響する
- 原材料の品質が規格に適合しているかを確認する
- 製造設備の点検
- ミキサーや計量機器などの設備が正確に機能しているかを定期的に点検する
- 必要に応じてメンテナンスを実施する
- 製造プロセスの管理
- 生コンの製造プロセスが規定通りに実施されているかを確認し、品質管理記録を適切に保持する
- 適切な配合と検査
- 生コンの配合は設計要求に応じて適切に行い、定期的な品質検査でその適合性を確認する
- 現場での適切な取り扱い
- 生コンの運搬、打ち込み、硬化過程の監視は、施工管理者の重要な役割
- 現場での迅速かつ正確な判断が品質確保の鍵となる
- 生コンは時間が経過するにつれ品質が変わる可能性がある
- 運搬中の振動や温度変化による品質の劣化にも注意が必要
- 問題発生時の対応
- 製造過程で問題が発生した場合、迅速に対応し品質に影響を与えないように処理する
- 記録の保持
- すべての検査結果と観察結果を記録し、将来の品質改善のためのデータとして利用する
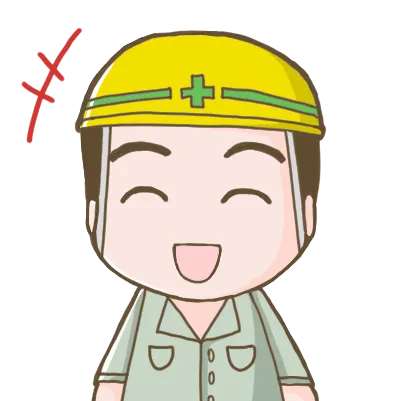
生コン工場との契約と発注に関して、もっと詳しい内容は以下の記事を参考にしてください。
関連記事 【現場監督必見】生コンの発注!上手な工場選びと契約のノウハウを徹底解説
現場に到着したコンクリートをよく観察する
生コンクリートが現場に届いたら、すぐに品質を確認することが大切です。
なぜなら、生コンクリート、通称「生コン」は、各ロット毎に品質のばらつきがあります。
各成分の量や品質、混ざるタイミング等によって、出来上がる生コンの硬さや耐久性が変わるのです。
品質のチェック方法は、まず、生コンの色を見ます。

色が一様でない、または通常と違う場合は、材料の混ざり方に問題があるかもしれません。
次に、手で触ってみます。
生コンは品質に問題がなければ、しっとりとしています。
もし手についた生コンがすぐに崩れたり、水分が多すぎてぬるっとしていたりすると、品質に問題がある可能性があります。
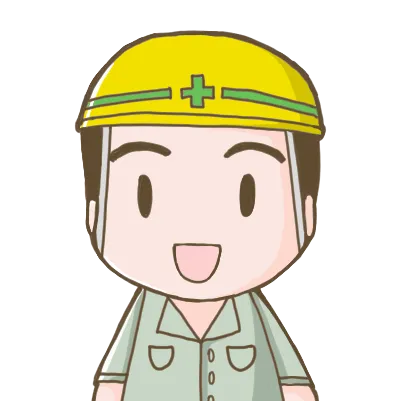
品質の良い生コンを見極める目を養うことで、建物の長寿命化や安全性向上につながります。
だからこそ、現場に届いた生コンの品質確認は重要です。
JIS A 5308 (レディーミクストコンクリート)では、コンクリートにおけ ある材料の計量誤差の許容範囲を下の 表のように定めています。
材料の種類 | 1回計量分量の計量誤差 |
---|---|
セメント | ±1% |
骨材 | ±3% |
水 | ±1% |
混和材 | ±2% |
混和剤 | ±3% |
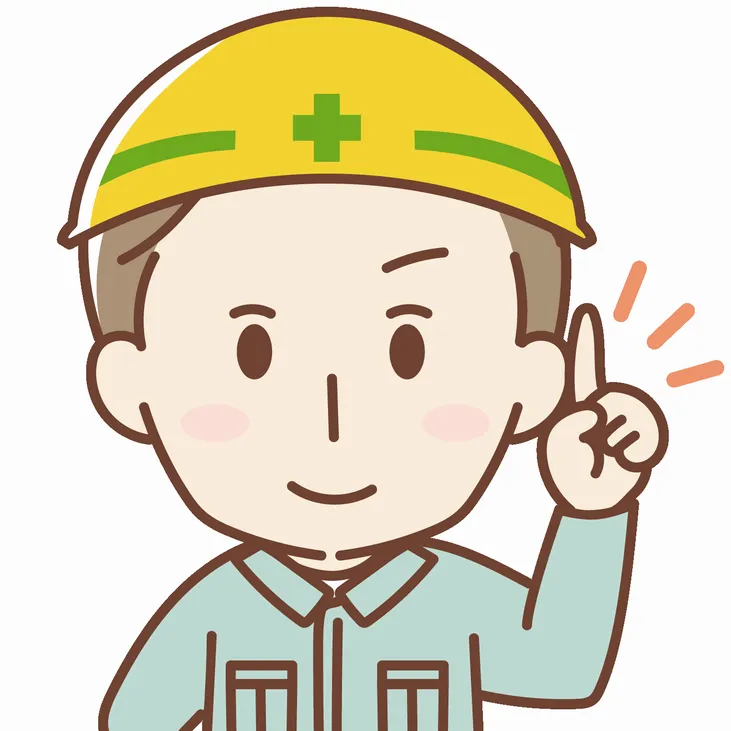
練り混ぜの1バッチごと、 または生コン車1台ごとで生コンの品質が多少異なることを想定しておきたいね。
また、 材料の品質変動・計量誤差・運搬の影響などを考慮して、 スランプの許容範囲(スランプ8cm以上18cm以下のコンクリートの場合±2.5cm)が設定されていることを頭に入れておきましょう。
コンクリートに使う細骨材と粗骨材には、内部に多少の空げきがあり、空げきの含水状態によって下の図に示すように4つの状態に分類できます。
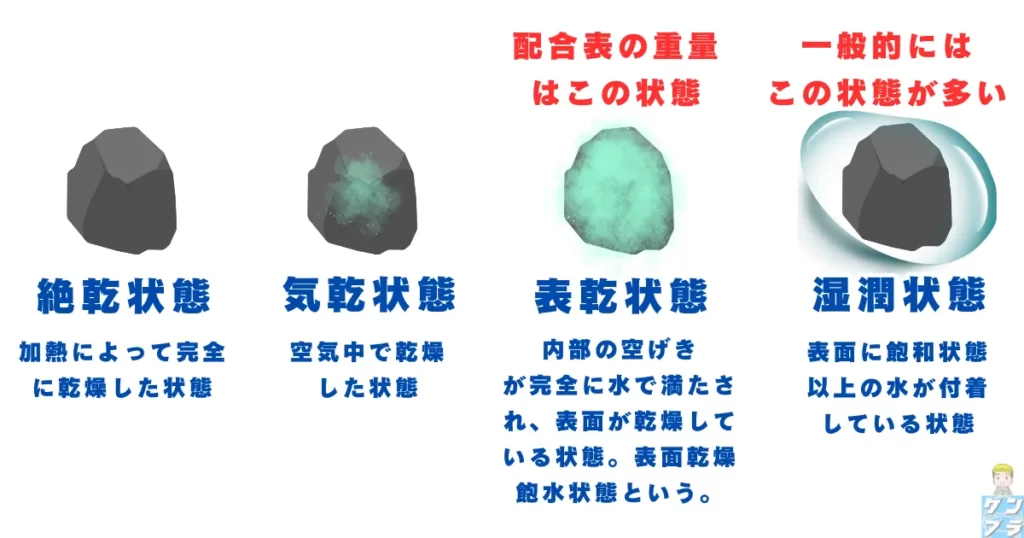
生コンが現場に到着したら出荷伝票も必ず確認しましょう。
生コンクリートは、工場から出荷されてから現場に届くまでの時間が品質に影響します。
出荷伝票には、出荷時刻とコンクリートの種類が記載されているので、それらを確認することで、注文したコンクリートが正しく、そして適切な状態で届いているかを判断できます。
たとえば、運搬時間が予定より長くかかってしまった場合、スランプロス(コンクリートが硬くなる現象)が大きくなる可能性があります。
これは、コンクリートが固まりやすくなっている可能性があるということです。
このような状況を早めに察知し、対応することが大切です。
出荷時のスランプを修正するように工場に連絡したり、打設手順を見直したりすることが考えられます。
また、工場は数カ所の現場に同時に出荷していることがあります。
そのため、違う現場向けのコンクリートが誤って運ばれてくる可能性もあります。
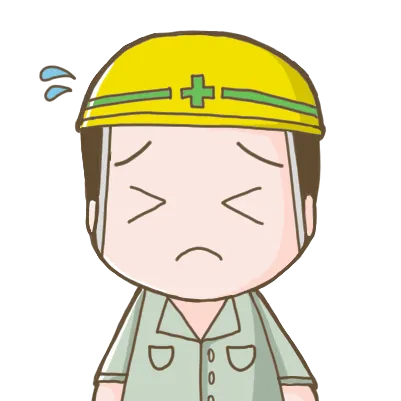
ありえないことだと思うかもしれませんが、生コン車の運転手がミスって現場を間違うこと、僕の現場で実際にあったんですよ。
関連記事 【コンクリートの品質管理】現場に到着したコンクリートをよく観察する
コンクリートの性質を考えて施工:ポンプ圧送時の管理
コンクリートのポンプ圧送性を評価する用語にポンパビリティという言葉が存在します。
圧送性は質の良し悪しを示す言葉ではありますが、具体的な定量的指標はまだ存在しません。
加圧ブリーディング試験や可視化試験など、いくつかの評価方法が試みられていますが、普及には至っていません。
圧送性は、「送りやすさ」と「閉塞しにくさ」の両面で評価されますが、これらに影響を与えるコンクリートの性質は対立することがあります。
たとえば、コンクリートの粘性が高い場合、材料分離が起こりにくくなりますが、輸送管内の摩擦抵抗が増加し、送り距離が長い場合に高圧での圧送が必要になり、送りにくくなることがあります。
適切な圧送性を持つコンクリートは、施工に適したスランプを備え、かつ分離しにくい適度な粘性を持っていることが求められます。
ポンプ圧送作業の計画を立てる際には、以下のポイントに注意が必要です。
- 圧送計画の策定
- 圧送を行う区画とポンプの設置場所を決定する
- コンクリートの性質を考慮してポンプの機種を選定し、圧送距離を予測する
- 圧送量の算定
- 1日の作業時間と打ち込み量から単位時間あたりの圧送量を計算する
- 作業効率や制約事項に合わせて最大圧送量を予測する
- 圧送時の配慮
- 圧送時の負荷を軽減するため、輸送管の無駄な経路を減らす工夫が必要
- ポンプの選定方法には、土木学会や日本建築学会、全国圧送事業団体連合会の指針が参考になる
- 基本的には所定の吐出量コンクリートが圧送されるときの管内摩擦から負荷を算出し、適切な機械を選定する
圧送作業中にも注意が必要です。
特に閉塞のリスクに注意しましょう。閉塞は作業時の連携ミスや不注意から発生することが多いため、工程の連携を確認し、困難な条件にも対応できるように準備しておくことが大切です。
また、輸送管内のコンクリートの流れについても理解しておく必要があります。
スランプの小さいコンクリートと粘性が高いコンクリートでは、流れ方が異なります。
特に粗骨材の分離に気を付け、均質な状態を保つ工夫が必要です。
ポンプ圧送作業は、確認事項をしっかりと把握し、計画的に行うことが成功の鍵です。
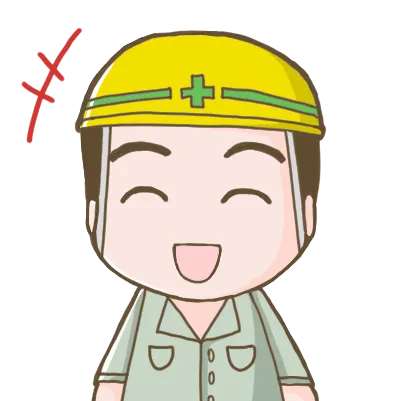
トラブルを最小限に抑え、効率的な施工を目指しましょう。
打設は材料分離を抑える:品質の良いコンクリートの施工方法
コンクリートはセメント、細骨材、粗骨材、水など、異なる材料で構成されています。
そのため、運搬や打ち込みなどの一連の作業中に、コンクリートを構成する材料が分離しやすくなります。
材料分離を抑えることが打ち込みの要点です。
材料分離とは、コンクリートを構成する材料の分布が均一でなくなる現象を指します。
たとえば、粗骨材が局所的に集中したり、水分がコンクリートの上部に向かって上昇したり、粗骨材が下部に沈んだりする現象です。
コンクリートを高い場所から落とすと、粒径の大きい粗骨材ほど分離しやすくなります。
下の図のようにシュートを使用してコンクリートを運搬すると、粒径の大きい粗骨材がモルタルよりも先に落ちて分離し、モルタルの割合が減少します。
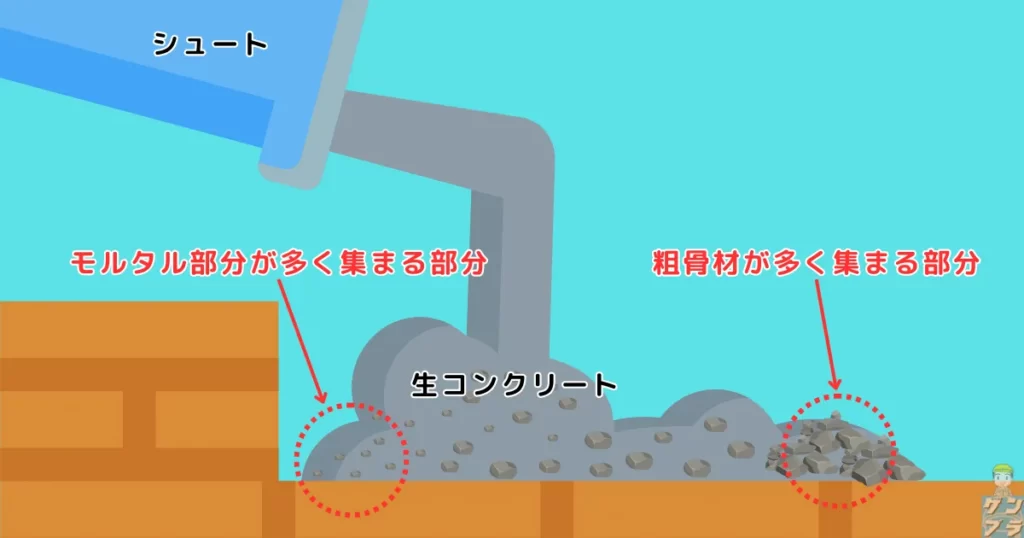
そのまま硬化すると、ジャンカ(豆板)などが発生し、外観の問題だけでなく、水密性や耐久性の観点からも問題が生じます。
コンクリートを打ち込んだ後に生じる材料分離の現象も存在します。
コンクリート内で、密度の高いセメント粒子や骨材が下に沈み、逆に、密度の低い水は比較的軽い微細な物質とともに上昇し、コンクリート表面に浮かび上がってきます。
この現象をブリーディングと呼び、浮上する微細な物質をレイタンスと呼びます。
ブリーディングに伴うコンクリートの沈降は、コンクリートを打ち込んだ後の1〜2時間程度に発生します。
この際、下の図のように鉄筋の位置に沿ってコンクリート表面にひび割れが生じることがあります。
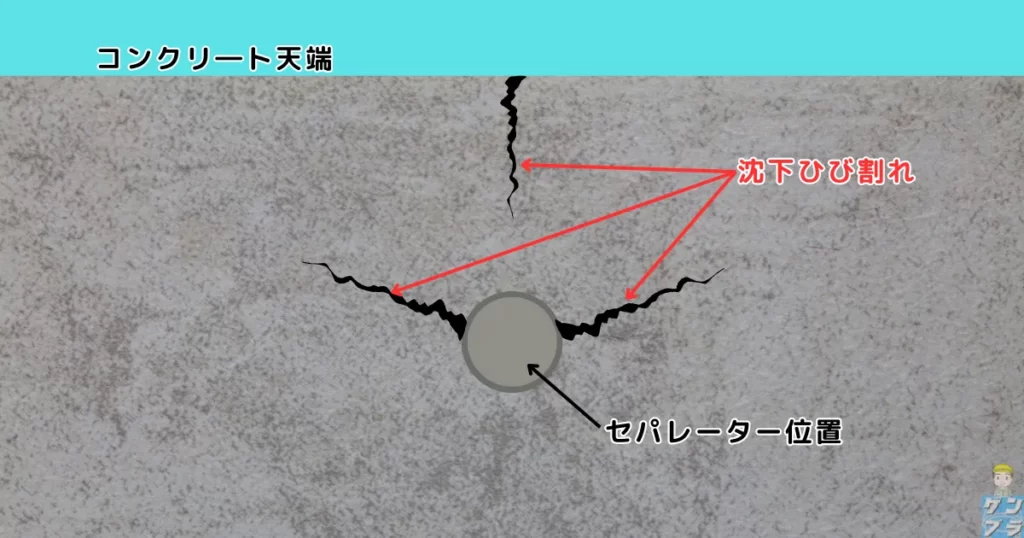
これは沈下ひび割れや沈み亀裂などと呼ばれ、ブリーディングが大きいコンクリートほど発生しやすいです。
このひび割れは一般的に鉄筋に達することが多いため、そのままにしておくと耐久性に影響を及ぼすことがあります。
そのため、ブリーディングが収まりつつある時に、コンクリート表面をコテを使ってたたいてひび割れを修理することが良いです。
ブリーディングは問題を引き起こすこともありますが、同時に表面から水分の急激な蒸発を防ぐ役割も果たします。
コンクリートを打ち込む際、鉄筋や型枠が動かないように十分な注意が必要です。
コンクリートの自由落下距離が大きいと、単なる材料分離だけでなく、落下の衝撃によって設計図に従って配置された鉄筋が移動したり、型枠がズレたり、かぶりを確保するために設置されたスペーサーが外れる危険性が生じます。
コンクリートの1層を厚くすると、下の部分が振動機で十分に締め固められず、ジャンカなどが発生する危険性が高まります。
したがって、内部振動機を使用する場合、1層の厚さを40〜50cm以下にすることが推奨されます。
コンクリートの打ち込み中に、さまざまなトラブルが発生する可能性があります。
そのため、トラブルに備えて対策を立てておくことが肝要です。
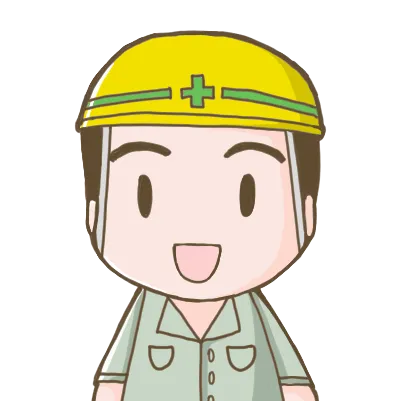
下表のチェック項目を参考に、生コン打設作業時のトラブルに備えましょう。
分類 | 項目 | 確認事項 |
---|---|---|
打ち込み前 | 打ち込み区画 順序、体制 | 打ち込み計画通りか |
型枠内の清掃 | 打ち込み箇所は清掃されており、異物や余剰水がないか | |
生コンクリートの発注 | 種類、打ち込み開始時間、数量に間違いないか | |
打ち込み機器類 | 計画したポンプ車が来ているか 配管径など配管計画通りか | |
打ち込み中 | 締固め機器 | 振動機の種類、本数、配置場所は計画通りか 予備の振動機の段取りができているか |
打ち込み体制 | 打ち込み責任者、受け入れ担当者はいるか | |
生コン工場との連絡体制 | 生コンの出荷速度の連絡体制はできているか (特に打ち込み終了間際の出荷量の調整) 生コンの異状や出荷の中断など緊急時の連絡体制ができているか | |
生コンの受け入れ検査 | 注文どおりの生コンが来ているか(納入伝票の確認) 運搬時間は適切か 品質を満足しているか 検査中の生コンを打ち込んでいないか 検査に立ち会っているか 受け入れ検査以外にもホッパーや筒先でコンクリートの状態を確認しているか | |
打ち込み手順 打ち込み方法 | 打ち込み手順は計画どおりか 打ち込み位置は計画どおりか 垂直に低い位置から落としているか(落下高さ1.5m以下か、材料分離していないか) 水平に打ち込んでいるか、横流ししていないか 1層の打ち込み高さは40~50cm以下か 打ち重ね時間は適当か ブリーディング水は処理しているか 生コンの供給と締め固め作業のバランスはよいか (供給過剰になっていないか、待ち時間が長くないか) 型枠支保工、配筋、スペーサーは正しい位置か 雨、風、直射日光に対する養生対策はしているか 照明器具など夜間作業時の準備はできているか | |
打ち込み後 | 沈みひび割れ | 沈みひび割れはないか、対処しているか |
養生 | 養生は計画通りになされているか |
関連記事 生コンクリート打設は材料分離を抑える!品質の良いコンクリートの施工方法を解説
失敗しない振動機(バイブレーター)の選び方とコツ
締め固めは、打ち込んだコンクリートを密実に仕上げるために欠かせない大切な工程です。
振動機の使い方を誤ったり、振動が不足したりすると、期待する締め固め効果を得られません。
逆に、振動を与えすぎても良いコンクリートになりません。
打ち込まれたコンクリートが型枠や鉄筋の隅々まで行きわたって鉄筋などとよく密着し、しかも密実に締め固められることによって、強度や耐久性のうえでも、優れた性能を発揮します。
コンクリートは打ち込まれる際に、エントラップトエアと呼ぶコンクリートにとって不要な空気を巻き込むため、その内部に径の大きな空げきが存在しています。
締め固めとは、振動を与えることによってこの不要な空げきを少なくし、密実なコンクリートとする作業です。
締め固め作業で一般的に用いる振動機は、コンクリートの中に挿入して使う「棒形振動機(内部振動機)」で、必要に応じて型枠に取り付けて使う「型枠振動機(外部振動機)」も利用します。
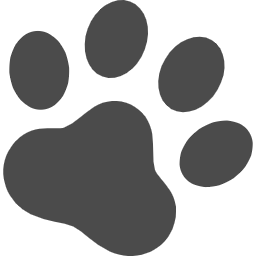
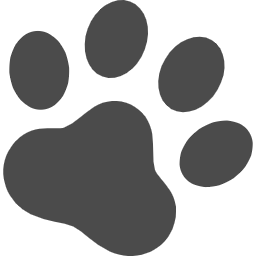
コンクリートに直接振動を加える方が効果的なことから、棒形振動機が広く普及しています。
土木学会のコンクリート標準示方書などでも、「コンクリートの締め固めには、内部振動機を用いることを原則とし、薄い壁など内部振動機の使用が困難な場合は型枠振動機を使用してもよい」としています。
振動機の締め固め能力はコンクリートの軟らかさなどによって異なります。
例えば棒形振動機の場合、小型振動機で1時間当たり4〜8m3、大型振動機で同じく10〜15m3程度。
下の図は、振動機の挿入深さを変えて締め固めたコンクリートの供試体のイメージ図です。
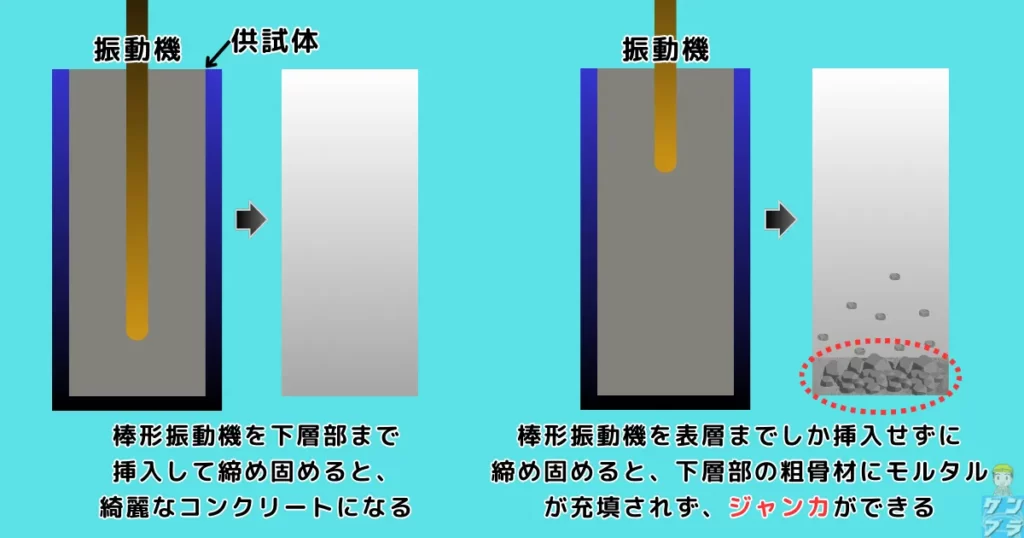
振動機の挿入深さが足りないと、振動が伝わらない下層部分に、締め固めが不十分な個所やジャンカができることがわかります。
きちんと内部まで振動機を挿入することが大切です。
コンクリートを打ち込む際に1層の厚さを厚くし過ぎると、振動機を内部まで挿入したとしても下層部まで十分な締め固めができない恐れがあります。
したがって、1層の厚さは振動機の振動部分の長さを超えないように注意すると良いです。
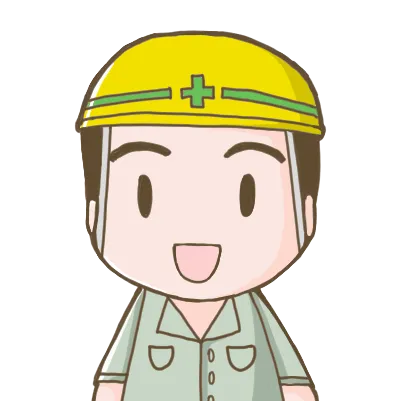
40〜50cm以下が一つの目安になります。
振動機を使う際のポイントは、できるだけ垂直に、一定の間隔で所定の深さまで挿入することです。
挿入間隔は50cm以下となるように配慮したいです。
振動機を引き抜く際はゆっくりと、孔が残らないようにすることも大事です。
特に、コンクリートを2層以上に打ち込む場合は、下の図に示すように振動機の先端を下層のコンクリートに10cm程度挿入して締め固めます。
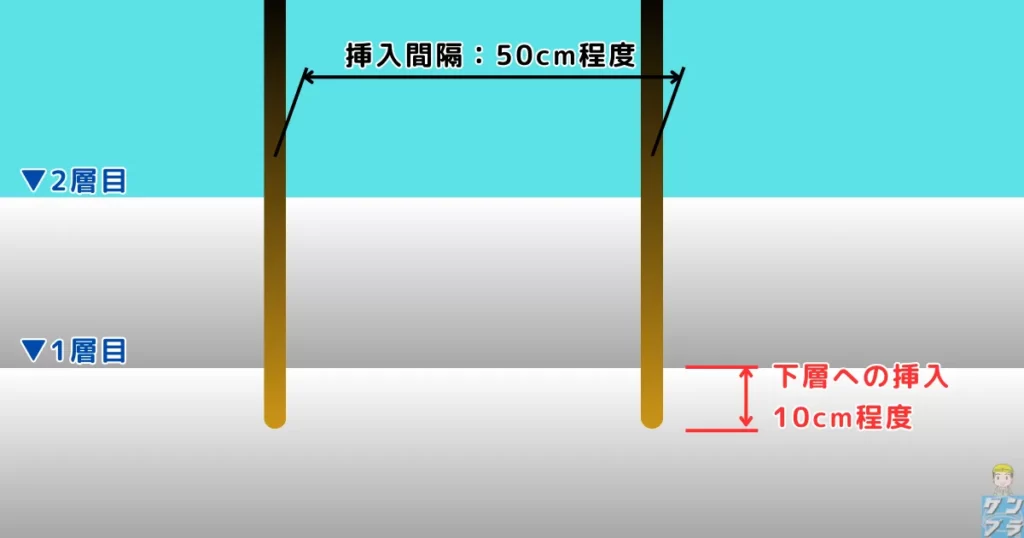
下層のコンクリートを振動によって再び流動化させ、上層コンクリートと下層コンクリートとを一体化することによって、コールドジョイントを防ぐことができます。
関連記事 失敗しない振動機の選び方とコツ:コンクリート締め固め作業のプロが伝授
コンクリート工事の成功法則:強度を決定する養生テクニック
コンクリートは、打設後も時間とともに品質が変わります。
適切に養生できるかどうかが、強度や耐久性を確保するうえで重要です。
養生のポイントや強度を予測する方法なども交え、施工段階で把握すべきコンクリートの強度特性や注意点について考えてみましょう。
コンクリート構造物の安全性や耐久性を確保するには、水セメント比や設計基準強度を適切に設定する必要がありますが、初期養生がそれらの性能を大きく左右することに注意しなければなりません。
コンクリート打設後の脱型に関連して、土木学会のコンクリート標準示方書では、強度の規格値として以下の2点を示しています。
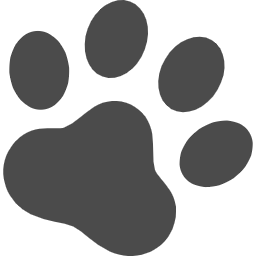
1つ目は、型枠や支保工の取り外しに必要なコンクリートの圧縮強度です。
施工時の安全性のほか、構造物の品質や性能を確保する目的で、下の表のように規定しています。
部材面の種類 | 例 | 圧縮強度 | コンクリートの
---|---|---|
厚い部材の鉛直または鉛直に近い面 傾いた上面 小さいアーチの外面 | フーチングの側面 | 3.5N/mm2 |
薄い部材の鉛直または鉛直に近い面 45度より急な傾きの下面 小さいアーチの内面 | 柱 壁 はりの側面 | 5.0N/mm2 |
橋・建物等のスラブおよびはり 45度より緩い傾きスラブ はりの底面 | スラブ はりの底面 アーチの内面 | 14.0N/mm2 |
例えば、コンクリートを型に流し込んだ後、側面に取り付けた型(型枠)を外すときは、コンクリートが重さや上に積まれる荷物に耐える強さを持つようになるまで、しっかりと時間をかけて成長させます。
施工現場では、これを「養生」と呼んでいます。
つまり、コンクリートがしっかりと固まり、自分の力で立てるようになるまで、時間をかけて大切に育てるんですね。
部材底面の型枠の場合は、上載荷重や自重による曲げ作用に対して抵抗し、部材に不具合が生じないレベルの強度が発現するまで養生する必要があります。
コンクリートが型枠に収まっている間は養生中とみなされます。
2つ目は、激しい気象作用を受けるコンクリートの養生終了時の所要圧縮強度です。
寒中コンクリートの初期凍害を防ぐために、養生温度を5℃以上に保つことを前提とし、養生終了時の圧縮強度を、断面寸法と構造物の露出状態で以下の表の通り規定しています。
構造物の露出状態 | 断面が薄い場合 | 断面が普通の場合 | 断面が厚い場合 |
---|---|---|---|
しばしば凍結融解を受ける場合 (次の春までの凍結融解が数10回程度) | 15N/mm2 | 12N/mm2 | 10N/mm2 |
まれに凍結融解を受ける場合 (次の春までの凍結融解が数回程度) | 5N/mm2 | 5N/mm2 | 5N/mm2 |
また、コンクリートの温度が急激に低下しないように所要の圧縮強度が発現した後も、2日間は0℃以上に保たなければなりません。
養生の終了時期を強度で決めるのは理にかなった方法ですが、実際には工事の途中で強度を見ながら養生を終えるのは少し複雑です。
だからこそ、強度の出方と養生日数の関係を知っておき、必要な強度に達するまでの日数だけ養生する方法が選ばれています。
セメントが水と反応すると、養生温度を上げると反応が速まり、早く強度が出るんですね。
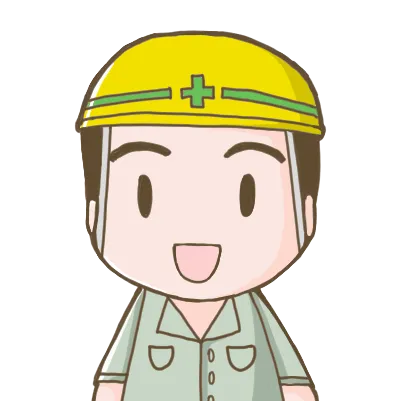
逆に、養生温度が低いと、強度の発現が遅くなります。
表の下に書かれているのは、通常のコンクリートの断面の大きさで考えた場合、初期凍害を防ぐために必要な養生日数の目安です。
これは、セメントの種類と養生温度の組み合わせによって示されています。
次の春までに想定される凍結融解の頻度 | 5℃以上の温度制御養生を行った後の養生温度 | 早強ポルトランドセメント(H) | 普通ポルトランドセメント(N) | 高炉セメントB種(BB) |
---|---|---|---|---|
しばしば凍結融解を受ける場合 (次の春までの凍結融解が数10回程度) | 5℃ | 5日 | 9日 | 12日 |
10℃ | 4日 | 7日 | 9日 | |
まれに凍結融解を受ける場合 (次の春までの凍結融解が数回程度) | 5℃ | 3日 | 4日 | 5日 |
10℃ | 2日 | 3日 | 4日 |
冬季は温度が低いので水和反応が阻害され、強度の発現が遅れます。
さらに外気温が-5℃程度以下になると、初期凍害を受けて所要の性能が得られない恐れがあります。
このような場合は、水和反応が円滑に進むように保温や給熱による養生を行う必要があります。
給熱養生にはジェットヒーターや蒸気のほか、面積が小さければ投光器や練炭を使うこともあります。
ジェットヒーターは一般的に使われていますが、使用する際は乾燥に注意しなければなりません。
温度を高める効果が大きい半面、熱風を供給することによって乾燥させてしまう恐れがあるからです。
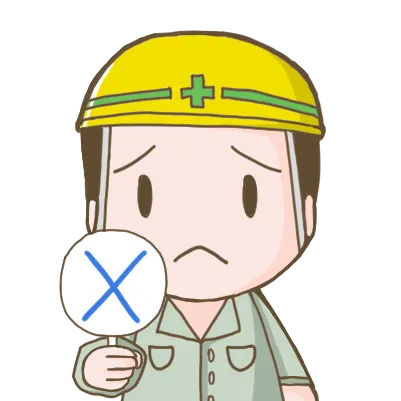
構造物の表面が乾燥してしまうと、ひび割れが発生するリスクがあります。
床などに散水して、十分な湿潤状態の下で給熱することが重要です。
関連記事 コンクリート施工の成功法則:強度を決定する養生テクニック
美しさと耐久性を兼ね備えたコンクリート構造物の秘訣
コンクリート構造物は構造や耐久性だけでなく、美しい外観も求められます。
外見の美しさは他の性能とも密接に関わり、型枠の各部分や打ち上げた表面にも潜在的な問題が生じる可能性があります。
コンクリート構造物が長期間にわたって所定の性能を維持するには、ジャンカ(豆板)や有害なひび割れなど美観に影響を与える不具合を回避する必要があります。
施工中または数日以内に発生する問題には、コールドジョイント、空洞、あばた、砂すじ、沈下ひび割れなどがあります。
また、時間の経過とともに内部拘束や外部拘束による温度ひび割れや乾燥収縮ひび割れなどが生じる可能性があります。
構造部位ごとに発生する不具合をまとめたものが下の表です。
構造物の部位 | 不都合の種類 | 発生原因 |
---|---|---|
梁、柱、壁などの鉛直面 | コールドジョイント | 打ち重ねの遅れ(打ち重ね時間間隔が長い) |
ジャンカ(豆板)、空洞 | 不十分な締固め | |
あばた | 表面部へのブリーディング水 空気泡の集中 | |
砂すじ | 型枠のすき間からの漏出 | |
沈下ひび割れ | 水平鉄筋、セパレーター位置の沈下 張り出し部など断面形状の違いによる沈下量の差 | |
温度ひび割れ | 断面内の温度差 | |
梁などの底面 | 型枠のたわみ | 不当沈下 支保工や型枠の変形 |
スラブなどの上面 | 沈下ひび割れ | 鉄筋位置上部とほかの部位と沈下量の差 |
プラスチック収縮ひび割れ | 日射、風などによる表面部の乾燥 |
スラブ上面の仕上がりを美しくするには、仕上げ作業のタイミングに留意する必要があります。
表面仕上げは、表面部付近の耐久性の確保、平たん性の確保、美観の確保のために非常に重要な作業です。
仕上げが早すぎると、ブリーディング水の影響を受け、遅すぎると手間がかかり、場合によっては発生した沈下ひび割れの適切な処理ができないこともあります。
ブリーディングが生じている早い段階で仕上げ作業をしても、その後のブリーディングによって沈下ひび割れが生じる危険もあります。
沈下ひび割れは、早い時期であればタンピングにより修復できます。
また、仕上げ作業時にブリーディング水を巻き込み、コンクリートの表面が脆弱になって、表面はく離やひび割れの原因となります。
逆に仕上げ時期が遅すぎると、打ち込んだコンクリートは凝結が進んで容易に平たん性が確保できないこともあります。
仕上げのタイミングは、打ち込むコンクリートのブリーディングの発生速度と凝結特性を考慮して決める必要があります。
ブリーディングや凝結のそれぞれの特性は、コンクリートの温度、雰囲気温度や雰囲気湿度、日射の有無、風などの影響を受けます。
これらの施工条件は各現場でまちまちであり、一義的に仕上げのタイミングを示すことはできません。
仕上げを請け負う会社の職人の経験に任せ切りなのが現状です。
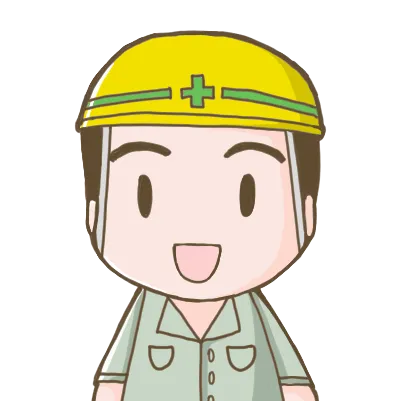
仕上げ作業の手順や注意すべき点については、施工管理を行う現場監督も理解しておきたいですね。
仕上げ作業の手順は、仕上げ面の性能に影響します。
コテ仕上げは、表面を平たんにするためだけでなく、鉄筋などの上部に発生する沈下ひび割れを修復することも目的としています。
したがって、凝結の特性を考慮してタイミングを見定め、一般には数回に分けて仕上げ作業を実施します。
以下に、コテ仕上げ作業の標準的な流れを示しています。
トンボなどのならし器具、桟木
所定の量のコンクリートを打ち込んだ後、大体のレベル出しをする
ブリーディングが収まった段階で平坦性を出す
凝結が始まり、表面が硬くなってきてから必要により数種類のコテを使って平滑性を出す
場合によっては金ゴテ仕上げを省略して、ほうき目仕上げをすることもある
関連記事 美しさと耐久性を兼ね備えたコンクリート構造物の秘訣とは?施工管理16年の現役現場監督が解説
鉄筋のかぶり確保術と最小かぶり・スペーサー個数
鉄筋工事は、設計図に基づくのが基本です。この遵守がコンクリート構造物の安全性や耐久性に直結します。
設計図を熟読し、かぶりを確実に確保することが重要です。
鉄筋工事の進行中に発生する可能性がある問題をまとめたのが下の表です。
原因 | 現象 |
---|---|
鉄筋保管の不備 | 鉄筋腐食 鉄筋表面の浮きさびによるコンクリートとの付着性能の低下 |
鉄筋加工の不備 | かぶり不足による鉄筋腐食 継ぎ手長不足 |
鉄筋の配置不良と定着の不備 | かぶり不足による鉄筋腐食 コンクリート打設時の鉄筋の移動 継ぎ手部付近のコンクリートのはく離 |
配筋の過密(設計基準変更に伴う) | コンクリートの締め固め不足による未充てん ジャンカやコールドジョイントの発生 |
配筋の不足 | 乾燥収縮ひび割れや温度ひび割れの発生 構造耐力不足 |
配筋間隔と骨材最大寸法の不適合 | コンクリートの未充てん ジャンカの発生 |
増設用接続鉄筋の長期暴露 | 接続鉄筋の顕著な腐食 |
スペーサーの不備 | かぶり不足による鉄筋腐食 鋼製スペーサーの使用による腐食 |
鉄筋の保管時、加工時、組み立て時など、あらゆる作業段階で鉄筋の腐食などのトラブルが潜んでいます。
鉄筋の腐食を防ぐには、精密なコンクリートを打ち込むだけでなく、鉄筋のかぶりを確実に保つことが不可欠です。
かぶりには、コンクリートとの付着強度を確保し、鉄筋の腐食を防ぐと同時に、火災時に鉄筋を保護する重要な役割があります。
コンクリート構造の安全と耐久性を築くための不可欠なプロセス、それが鉄筋工事です。
設計図は設計者の意図を明確に表現したものであり、施工者はその情報どおりにつくるのが原則です。
設計図は本来、十分に検討されて問題のない状態で施工者に渡さなくてはなりませんが、現状では残念ながらそうでない場合が見られます。
施工計画段階で、配筋上の課題をはじめ設計図の問題点を事前に見つけて、その対策を取ることができるかが、品質の良い構造物を構築するうえで重要です。
そのためには設計図のチェックの仕方がポイントになります。
図面どおりに組み立てられない場合があるという意識で、下の表に示すような内容に注意しましょう。
- 曲げやフック形状が省略されて描かれていないかどうかチェックする。
- 鉄筋は1本の線で描かれているが、実際には太さがあり節もある。太さを持たせた詳細図を描いてチェックするのが望ましい。
- 複数の部材の接合部では、相互の鉄筋の干渉や、定着フックの納まりをチェックする
- 重ね継ぎ手では、相互の鉄筋の位置はずれる。また、機械式継ぎ手部では母材よりも太くな ることに注意する。
- コンクリートの打設個所やバイブレーターを挿入するあきが考慮されているかをチェックする
- 鉄筋の図面だけでなく、ほかの図面も重ね合わせてよく見る。
- コンクリート打ち継ぎ位置(鉄筋継ぎ手位置)と山留め支保の高さの関係
- 埋設する仮設構造物はないか
- プレストレスト鉄筋コンクリート造ではケーブルシースと鉄筋の干渉を確認
- 埋設管や箱抜きがある場合の鉄筋処理方法が示されているか
設計図では柱や梁などの部材の配筋図は別々に記載されており、鉄筋相互の関係がチェックされていないことがあります。
鉄筋相互の干渉や鉄筋のあきなどをチェックする方法として、二次元の各配筋図を組み合わせて鉄筋の太さを持たせた三次元で表現できるCAD技術もあります。
図面を確認して洗い出した問題点は、施工計画段階で解決しておくことが重要です。
密度がそれほど高くない配筋であれば、現場合わせで対処可能です。
しかし、高密度の配筋では組み立て精度が悪いと、鉄筋の配置が不可能となってしまったり、設計で意図した性能を確保できない鉄筋の配置となってしまったりすることがあります。
やむをえず鉄筋の配置を変更する際には、設計で要求される性能を確保することが前提となりますので、各鉄筋の役割と配置条件をよく理解しておく必要があります。
変更案の採用に当たっては設計者の判断を仰ぐのがよいでしょう。
鉄筋加工寸法は施工誤差の許容値(下の図参照)を考慮して設定します。
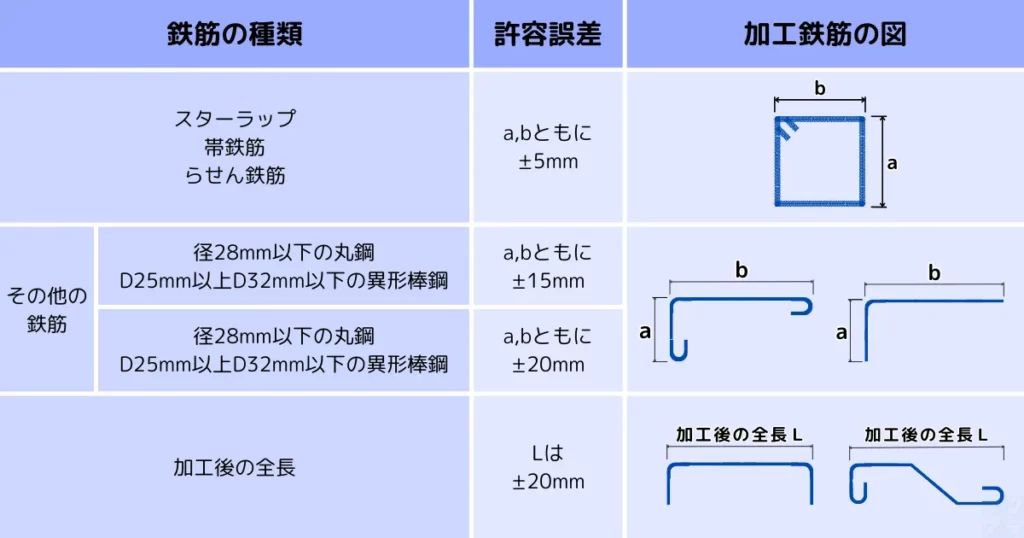
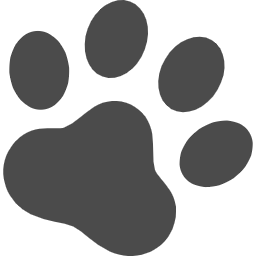
配筋の際には、鉄筋を正しい位置に組み立て、鉄筋のあきとかぶりを確保します。
鉄筋のあきは、下の図に示すように、互いに隣り合って配置された材の外側と外側の距離を指します。
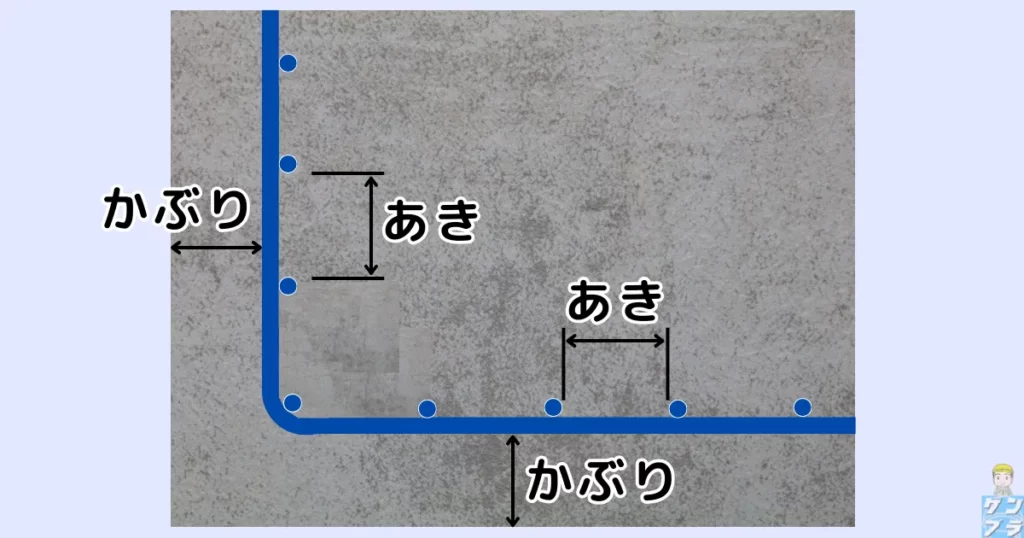
鉄筋とコンクリートが付着することで応力が十分に伝達されるように、コンクリートを充てんできる間隔を確保します。
組み立てた鉄筋の上を作業員が歩く際やコンクリートの打設時に、鉄筋が移動するのを防ぐために、鉄筋同士を結束します。
結束線と呼ばれる直径0.8mm以上の鉄線を使うのが一般的であり、またクランプと呼ばれる金具も使用されます。
結束線はかぶり部分に入らないように内側に曲げておくことが大切です。
かぶりは通常、鋼材またはシースの表面からコンクリート表面までの最短距離を指します(下の図参照)。
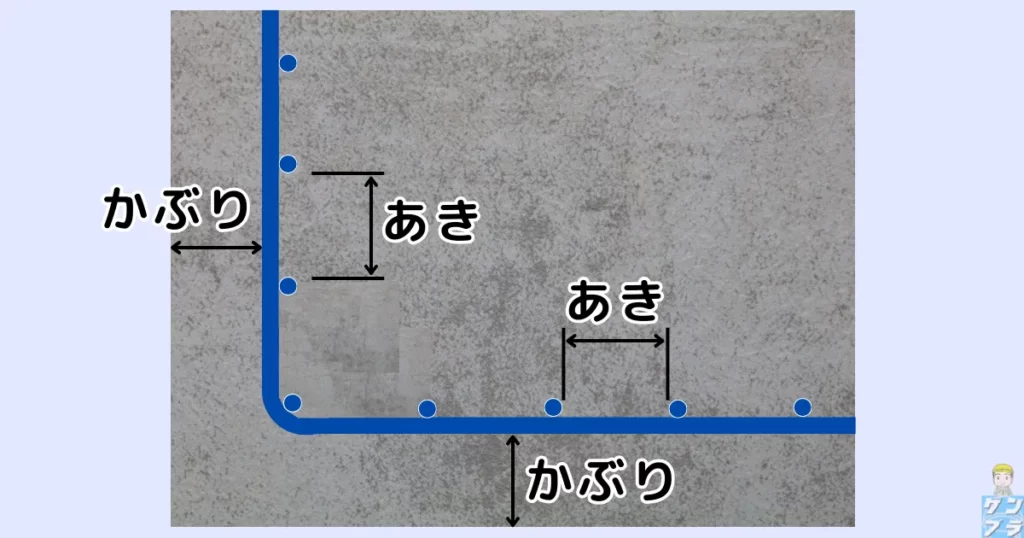
設計図上のコンクリート表面から鉄の中心までの距離ではないことに注意してください。
かぶりは、コンクリートの品質、鉄筋の直径、構造物の環境条件、コンクリート表面に作用する有害な物質の影響、部材の寸法、施工誤差、構造物の重要度などを考慮して定めます。
設計上の鉄筋のかぶりは、下の表に示すように、鉄筋の直径または耐久性を満足するかぶりのいずれか大きい値(耐火性を要求しない場合)に施工誤差を加えた値(かぶりの最小値)以上となるように設定します。
W/Cの最大値 | かぶりCの最小値 | 施工誤差ΔCe | |
---|---|---|---|
柱 | 50mm | 45mm | ±15mm |
梁 | 50mm | 40mm | ±10mm |
スラブ | 50mm | 35mm | ±5mm |
橋脚 | 55mm | 55mm | ±15mm |
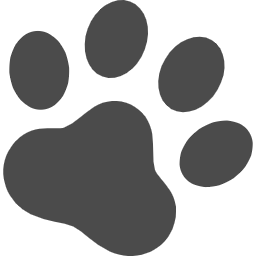
この表では、塩害が厳しくない一般的な環境下において、普通ポルトランドセメントを用いて、設計耐用年数を100年と仮定した場合に、耐久性の照査をしなくても不都合が生じないと考えられる標準的なコンクリートの品質とかぶりの組み合わせを示しました。
かぶりの確保は、耐久性のためには最も重要です。
確実に確保するには、スペーサーを適切に使うのがよいです。
さまざまなスペーサーが市販されているので、用途に合わせて適切なものを選定してください。
よく使われるスペーサーには、コンクリート製またはモルタル製、プラスチック製、鋼製があります。
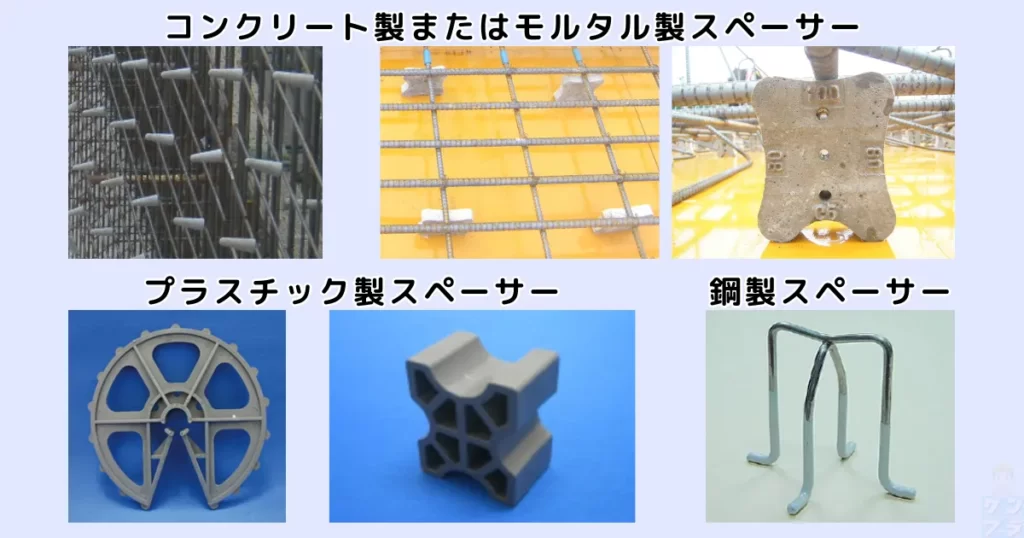
型枠に接する個所には、耐久性の観点からコンクリート製またはモルタル製のスペーサーを使うのがよいです。
その際、本体コンクリートと同等以上の品質のものを選ぶことが重要です。
鋼製スペーサーは剛性が高く変形しにくい特徴があり、型枠に接する部分は防錆塗料などで処理されていますが、耐久性の面で弱点となりやすいです。
特に海岸付近のように腐食環境の厳しい地域では、鋼製スペーサーを使わないのが賢明です。
ドーナツ型のプラスチック製スペーサーは、柱や壁に使うことが多いです。
ただし、プラスチックはコンクリートと熱膨張係数が異なり、付着力や耐荷力が不足し、耐火性に欠けるといった問題があります。
スペーサーは水平筋に設置し、鉛直筋には設置しません。
鉛直筋に設置すると、打設に伴うコンクリート荷重が作用してスペーサーが変形したり、スペーサーの下側にブリーディング水がたまったりするからです。
スペーサーに作用する荷重は、スペーサーの設置場所により異なります。
壁や柱では、スペーサーに作用する荷重を特に考慮しなくてもよいです。
一方、スラブなどの水平鉄筋用スペーサーには、鉄筋やコンクリートの荷重と、配筋時やコンクリート打設時の作業荷重が作用します。
スペーサーの数が不足すると、打設時の荷重で鉄筋のたわみが大きくなったり、スペーサーの位置がずれたりして、所定のかぶりを確保できません。
設置するスペーサーの個数は、構造物の底面では1m2当たり4個以上、側面では1m2当たり2個以上が標準となります。
- 構造物の底面・梁…1㎡当たり4個以上
- 構造物の側面・柱…1㎡当たり2個以上
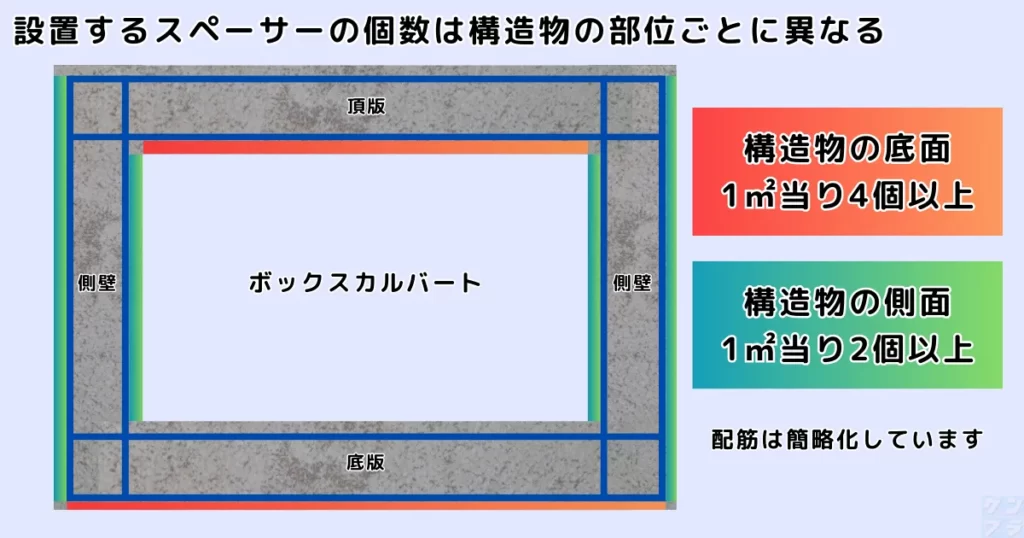
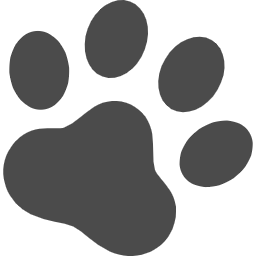
スラブなどで、スペーサーを設置する面の不陸が大きい場合は、スペーサーに作用する荷重がさらに不均一となるのでスペーサーの数を増やすことも検討したいです。
特に、梁ハンチ部分はかぶりが不足しやすい個所なのでスペーサーを増やすなどの対策が必要です。
ただし、スペーサーの個数を増やすとかぶりの誤差は小さくなる一方で、スペーサーは劣化因子の侵入路となる可能性があるので、むやみに増やすことは控えるべきです。
スペーサーの設計や施工の検討には、日本土木工業協会が1994年3月に発行した「鉄筋工事用スペーサー設計・施工ガイドライン」が参考になります。
鉄筋の加工と組み立てが終了し、コンクリートを打設する前に、鉄筋の本数、折り曲げ位置、継ぎ手の位置と長さ、鉄筋相互の位置と間隔などが、設計図に基づく所定の精度でできているかを検査します。
鉄筋工事の検査項目には、下の表のようなものがあります。
項目 | 試験・検査方法 | 時期・回数 | 判定基準 | |
---|---|---|---|---|
鉄筋の種類・径・数量 | 製造会社の試験成績表による確認 目視、径の測定 | 加工後 | 設計図書どおりであること | |
鉄筋の加工寸法 | スケールなどによる測定 | 所定の許容誤差以内であること | ||
スペーサーの種類・配置・数量 | 目視 | 組立後および組立後長期間経過した時 | 底面・梁などで1㎡あたり4個以上、底面・柱などで1㎡当たり2個以上 | |
鉄筋の固定方法 | 目視 | コンクリートの打ち込みに際し、変形・移動のおそれがないこと | ||
組 み 立 て た 鉄 筋 の 配 置 | 継手及び定着の位置・長さ | スケールなどによる測定 および目視 | 設計図書どおりであること | |
かぶり | 耐久性照査時で設定したかぶり以上であること | |||
有効長さ | 許容誤差:設計寸法の±3%または±30mmのうち小さいほうの値(標準) | |||
中心間隔 | 許容誤差:±20mm(標準) |
同じ構造物でも、発注機関によってかぶりの基準値の許容範囲が異なる場合があります。
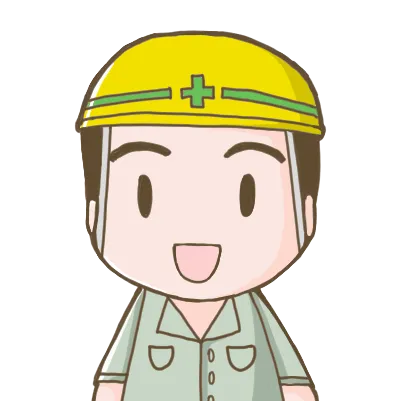
発注機関の「共通仕様書」から規格値は事前に必ず確認しておきましょう。
関連記事 耐久性UP!鉄筋のかぶり確保術と最小かぶり・スペーサー個数を解説
コメント